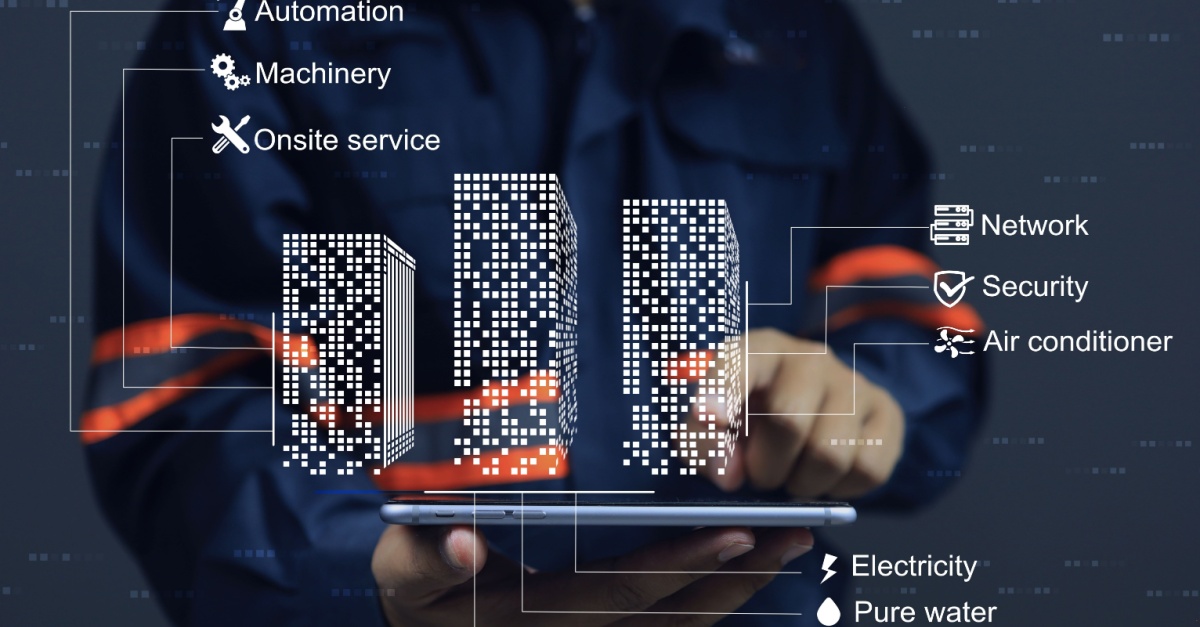
Future-Focused Facilities Management: Leveraging Technology for Effective Facility Maintenance
April 30, 2025
Every facility tells a story — and the most successful ones are written with data, not guesswork. As the industry evolves, senior facility management professionals are facing increased pressure to drive efficiency, cut operational costs, and keep their buildings performing at peak levels. Meeting these demands requires more than just experience; it demands a forward-thinking, tech-enabled approach.
By leveraging tools like IoT, AI, mobile platforms, and cloud-based systems, facility teams can move from reactive maintenance to predictive strategies that prevent issues before they arise. In the following sections, we’ll explore the technologies and best practices reshaping facility maintenance management, equipping leaders with the insights they need to optimize performance and build future-ready operations.
1. Why Future-Focused Facility Management Matters
In today’s fast-evolving commercial landscape, occupant expectations have shifted dramatically. Tenants, employees, and guests now view facilities through a customer-centric lens, expecting environments that are not only safe and well-maintained but also integrated with smart, user-friendly technologies. Comfort, indoor air quality, and seamless digital experiences are no longer luxuries — they’re baseline expectations.
This evolution puts a spotlight on the steep cost of reactive maintenance. Waiting until something breaks not only risks occupant dissatisfaction but also leads to costly emergency repairs and unplanned downtime. In contrast, predictive and proactive maintenance — fueled by IoT sensors, AI diagnostics, and automated alerts — helps detect issues early, minimize disruptions, and significantly extend asset life cycles.
Adopting future-focused tools also unlocks new levels of operational efficiency. Cloud-based platforms and mobile solutions enable real-time decision-making, while data analytics identify trends that drive smarter resource allocation. For senior facility leaders, investing early in these technologies isn’t just about modernization — it’s a long-term strategy to reduce costs, enhance performance, and maintain a decisive edge in an increasingly tech-forward industry.
2. Harnessing the Power of IoT for Predictive and Preventive Maintenance
Modern facilities are undergoing a technological transformation, with IoT sensors playing a critical role in monitoring systems like HVAC, lighting, elevators, and security. These devices capture real-time data on temperature fluctuations, vibration levels, energy usage, and more, providing a 24/7 snapshot of equipment health and improving facility maintenance management.
With this continuous stream of data, facilities can shift from reactive to predictive maintenance. Smart algorithms analyze trends to detect anomalies before failures occur, and automated alerts can trigger service orders the moment equipment deviates from optimal performance thresholds. For instance, predictive HVAC monitoring has been shown to reduce maintenance costs by up to 25% and cut downtime by nearly 50% in some case studies.
Occupants now expect seamless, tech-integrated spaces. The pressure is on facility managers to meet higher standards for comfort, safety, and responsiveness. Reactive maintenance not only increases emergency repair costs but also disrupts the occupant experience. IoT-powered, proactive strategies extend equipment life and minimize disruptions — delivering measurable ROI. Embracing this digital shift early positions organizations for sustainable, long-term efficiency gains.
3. Data Analytics: Turning Information into Actionable Insights
Today’s facility managers need more than spreadsheets — they need real-time, actionable insights that help drive smarter decisions. That’s where structured data and advanced analytics come in. By leveraging cloud-based dashboards, managers can get a clear picture of facility performance at a glance, tracking everything from energy consumption and asset downtime to how quickly work orders are being completed.
Key performance indicators (KPIs) like those not only help measure success but also uncover where inefficiencies may be hiding. Is a certain asset requiring more repairs than usual? Are energy costs slowly creeping up month over month? With the right data, you can get ahead of these issues before they become budget busters.
Implementation starts with choosing the right analytics platform — one that can be customized to your facility’s needs. From there, it’s all about training your team to read the data and use it to align facility maintenance management strategies with what’s actually happening on-site. In short, when your data talks, listen.
4. The Rise of Cloud-Based Facility Management Platforms
Cloud-based facility maintenance management platforms have revolutionized how teams monitor and maintain building operations by providing centralized, real-time access to data across multiple sites and assets. These platforms offer live updates on maintenance requests, asset health, and inventory levels, allowing for faster response times and more accurate planning.
As organizations expand, cloud platforms scale effortlessly, whether adding a new facility or integrating enterprise systems like ERP, HR, or accounting. This creates a unified ecosystem in which operational data is not siloed but instead contributes to a comprehensive view of organizational performance.
Security remains paramount, with leading platforms adhering to stringent protocols such as encryption, multifactor authentication, and automated backups. Built-in disaster recovery features ensure operational continuity even during critical failures.
Beyond data collection, these systems unlock data intelligence. Dashboards and visual KPIs — such as energy consumption, asset downtime, and work order completion rates — help identify inefficiencies and guide resource allocation. To implement effectively, facility leaders should select platforms with customizable analytics and prioritize staff training to translate insights into actionable facility maintenance management strategies.
5. Enhancing Collaboration and Accountability Through Mobile Solutions
Mobile-first maintenance workflows are transforming how facility teams operate, especially when armed with tablets or smartphones. Technicians can instantly access work orders, asset histories, and equipment manuals on-site, minimizing delays and reducing the dependency on outdated spreadsheets and paperwork. This streamlined approach accelerates task completion and eliminates the risks associated with misplaced or incomplete documentation.
Real-time communication tools embedded in mobile platforms — such as in-app messaging and push notifications — keep technicians, vendors, and management in sync. These features allow teams to make quick, informed decisions based on live updates from the field, whether it’s approving emergency repairs or rerouting labor to a higher-priority task.
Perhaps most importantly, mobile solutions enhance transparency and accountability. As status updates are logged and visible to all relevant stakeholders, it becomes easier to track progress, verify completion, and meet compliance requirements. Clear audit trails and digital documentation ensure that every step of the maintenance process is recorded, helping senior facility leaders maintain both operational integrity and regulatory readiness.
6. Focusing on Sustainability and Energy Management
As corporate and regulatory pressure mounts to adopt greener operations, sustainability is no longer optional — it’s a strategic advantage. Eco-conscious facility operations directly impact both brand reputation and bottom lines, such as LEED-certified buildings reporting nearly 20% lower maintenance costs than typical commercial buildings. Companies are increasingly being judged by their environmental footprint.
Green building initiatives such as LEED certification and WELL Building Standards are shaping how modern facilities are designed and maintained. Facility leaders are embracing tools that track energy consumption, water usage, and waste reduction, using real-time data to optimize resources and reduce inefficiencies. These efforts contribute to long-term savings through lower utility bills, prolonged equipment lifespans, and eligibility for tax credits or green incentives.
Many organizations have already reaped measurable rewards, like reducing HVAC energy use through AI-powered analytics or cutting water waste with IoT-enabled sensors. Meanwhile, mobile-first maintenance workflows empower technicians with instant access to asset histories, work orders, and checklists on-site, minimizing paper trails and delays. Real-time communication features — like in-app messaging — accelerate coordination, improve transparency, streamlining facility maintenance management, and ensure every task is logged, traceable, and compliant with evolving sustainability standards.
7. Embracing Emerging Tech: AI, Robotics, and Immersive Tools
Integrating artificial intelligence into facility maintenance transforms reactive processes into smart, automated systems. AI-powered platforms can handle scheduling, analyze data trends for predictive maintenance, and allocate resources with precision. Chatbots and virtual assistants also play a growing role by triaging service requests and routing them efficiently, minimizing delays and freeing up staff for high-priority tasks.
Robotics and drones are revolutionizing facility maintenance management by tackling labor-intensive or hazardous duties. From robotic floor cleaners and autonomous security patrols to drones conducting high-rise inspections, these technologies improve safety, reduce downtime, and boost efficiency in hard-to-reach or high-risk environments.
Meanwhile, augmented and virtual reality tools are elevating workforce training and on-the-job performance. VR simulations offer immersive, low-risk environments for skill-building, while AR overlays can guide on-site technicians through repairs with real-time visual instructions. These innovations not only streamline operations but also close skill gaps and reduce human error.
Together, AI, robotics, and immersive tools position facility leaders to meet rising demands for smarter, faster, and safer building management strategies.
Future-Proofing Your Facility Starts with a Forward-Thinking Partner
In an era when efficiency, longevity, and cost savings define success, forward-thinking facility maintenance demands a shift toward proactive, tech-driven strategies. By integrating predictive tools, IoT devices, AI-driven insights, and cloud-based systems, facility managers can uncover inefficiencies, extend asset lifespans, and reduce operational costs. Mobile solutions and real-time data analytics not only streamline workflows but also empower teams to act before issues escalate.
At BrandPoint Services, we leverage predictive tools, IoT technology, AI-driven insights, and cloud-based platforms to help facility managers uncover inefficiencies, extend asset lifespans, and lower operational costs. Our mobile solutions and real-time data analytics streamline workflows and equip your teams to resolve issues before they escalate.
We specialize in nationwide facility maintenance, repair, refresh, and renovation programs tailored to your unique operational needs. With scalable solutions and a commitment to excellence, we help you move from reactive to resilient.
Connect with BrandPoint Services today to discover how our future-ready maintenance strategies can transform your facilities into smarter, stronger assets.